This particular course entitled “Two-Phase Pipe Hydraulics & Pipe Sizing” under the specialization entitled “Design of Industrial Piping Systems” is mainly aimed at predicting the two-phase total static pressure drop in a given piping system when both gas and liquid flow through it concurrently. Pressure drops including heat transfer coefficients depend on two-phase flow regimes since two-phase patterns and local internal structure are different for different flow regimes. Therefore, the formation of various two-phase flow regimes in horizontal and vertical pipes is to be known to the designer, and at the same time, the influence of bend on the formation of two-phase flow regimes in upstream and downstream pipes should also be known. The presence of a bend is inevitable in the piping systems of a plant and its presence restricts the formation of certain two-phase flow regimes commonly found in individual horizontal and vertical pipes for the given flow rates of gas and liquid and pipe diameter. Surprisingly, bend allows the formation of slug flow regimes in both horizontal and vertical pipe runs of a piping system. This is a nerve-wracking issue for the designer since the slug flow regime harms the piping system and in some situations, the slug flow regime becomes the main cause of the failure of the piping system. Therefore, the designer should be cautious during the design of two-phase piping systems and avoid the slug flow regime formation at any cost while designing the two-phase piping system.

This Labor Day, enjoy $120 off Coursera Plus. Unlock access to 10,000+ programs. Save today.

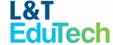
Two-Phase Pipe Hydraulics and Pipe Sizing
This course is part of Design of Industrial Piping Systems Specialization

Instructor: Subject Matter Expert
1,832 already enrolled
Included with
(12 reviews)
Recommended experience
Skills you'll gain
Details to know

Add to your LinkedIn profile
4 assignments
See how employees at top companies are mastering in-demand skills
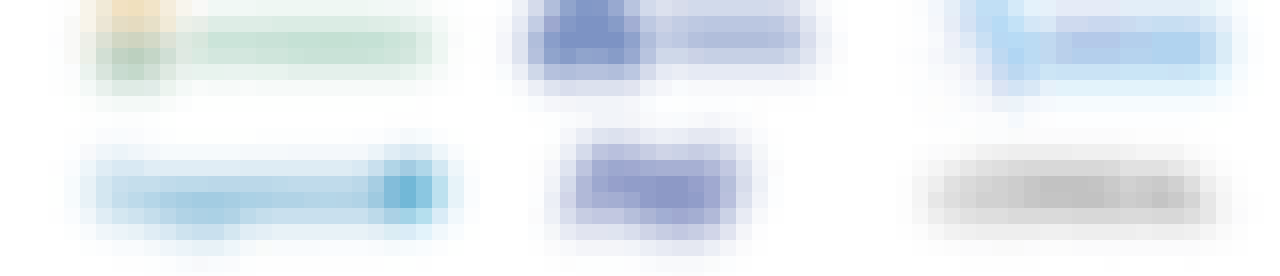
Build your subject-matter expertise
- Learn new concepts from industry experts
- Gain a foundational understanding of a subject or tool
- Develop job-relevant skills with hands-on projects
- Earn a shareable career certificate
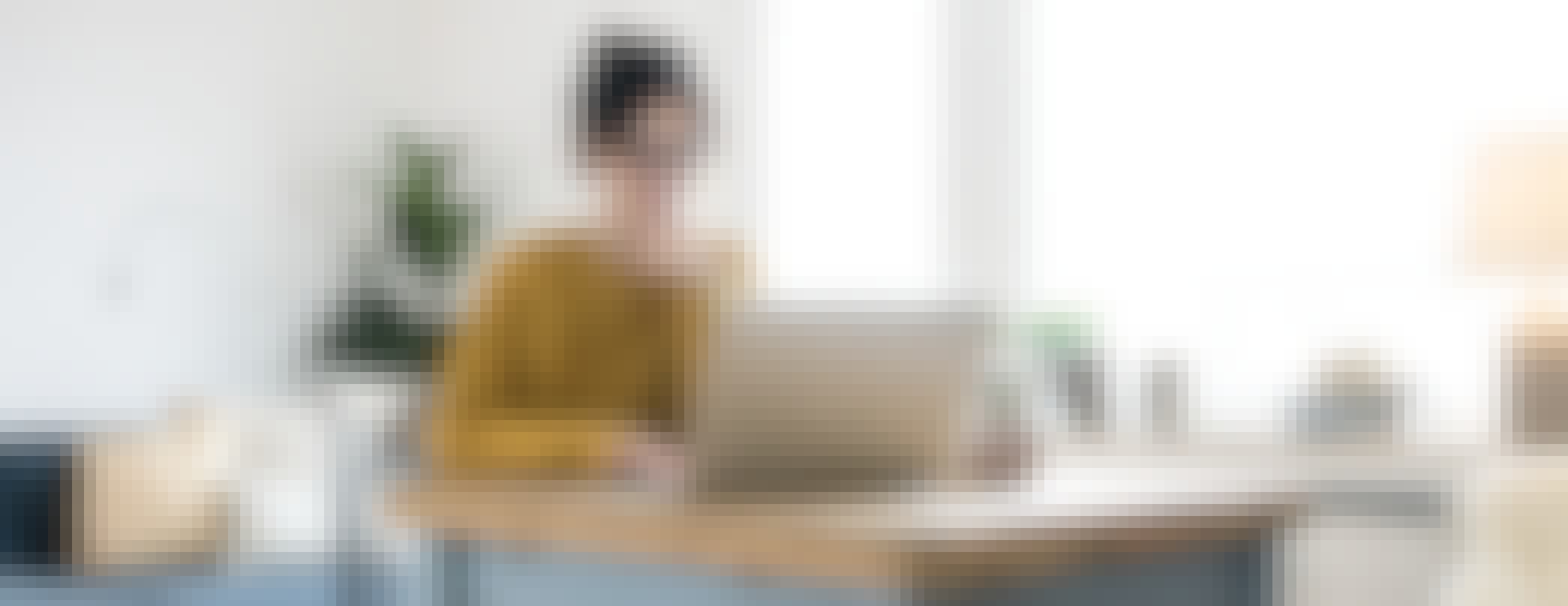
There are 4 modules in this course
Most of the piping systems in the oil and gas, chemical, and process industries are subjected to two-phase flow, especially liquid and gas. Based on the diameter and inclination of the pipe, and liquid and gas flow rates, various types of flow regimes occur in the pipe. One can find the types of flow regimes such as bubbly, stratified, stratified wavy, plug, slug, annular, and mist in a horizontal pipe, and bubbly, slug, churn, annular, and mist in vertical pipes. Identification of these two-phase flow regimes is very important which helps in identifying the pattern and internal structure of two-phase flow. Each pattern has a specific characteristic. Pressure drops and heat transfer coefficients are directly connected to this two-phase pattern and local internal structure. Bends are used to divert the flow and form the piping systems as per the piping layout. The bend of a piping system influences two-phase flow regime formation both in horizontal and vertical pipe legs and the expected two-phase flow regime in horizontal pipe alone and vertical pipe alone may not occur in horizontal and vertical pipe legs of a piping system connected by a bend. Therefore, identifying the two-phase flow regime is an important feature in designing the piping system for the given liquid and gas flow rates. This module is dedicated to the identification of flow regimes in horizontal pipe alone and vertical pipe alone using flow pattern maps, to understand two-phase flow regime formations in horizontal and vertical pipe legs in the presence of bends of a piping system, and to explain the two-phase terminologies such as mass quality, void fraction, mass velocity, volumetric quality, and superficial velocity. The relations among these terminologies are covered which assists in predicting the pressure drop in turn the design of piping systems.
What's included
17 videos1 reading1 assignment
Two-phase gas and liquid flow is not well established the way the single-phase is established. One can find well-accepted frictional factor correlations for turbulent flow and an analytically derived friction factor correlation for laminar flow. Since both gas and liquid concurrently flow through the pipe and different two-phase flow regimes form in a pipe, the single-phase frictional factors cannot be used directly to predict the pressure drop and design the piping system. One way of dealing with the two-phase gas and liquid flow is to use the single-phase friction factors to determine the frictional pressure drop by considering both gas and liquid are well mixed and flow through the pipe with the same velocity. No relative velocity exists between gas and liquid. The well-mixed gas and liquid become a pseudo-fluid. This fluid has neither the physical properties of gas nor liquid. The physical properties are density, dynamic viscosity, etc. The model that is developed based on the well-mixing of gas and liquid assumption is the Homogeneous Equilibrium Model, HEM. Here, the density and viscosity of a two-phase mixture determination is on the weight basis of the presence of gas and liquid in the two-phase mixture. The developed HEM is the inclusion of frictional pressure drop, accelerational pressure drop, and gravitational pressure drop. The existence of gravitational pressure drop is due to the inclination of the pipe. The homogeneous density of the two-phase mixture and void fraction are the parameters required to determine the gravitational pressure drop. As the gas phase is involved and the piping system is operated at higher pressures, the resulting pressure drop due to the compression of the gas needs to be considered in a two-phase flow. This pressure drop is nothing but an accelerational pressure drop. Coming to the frictional pressure drop, this term contains an important parameter, the ‘two-phase friction factor’. Without knowing this parameter, the determination of a two-phase frictional pressure drop is not possible. As said single-phase friction factor correlations are available and one can take advantage of these friction factor correlations. It is possible when the liquid phase is assumed to flow alone through the pipe with the two-phase mixture flow rate. However, two phases, ‘gas and liquid’ flow through the pipe, to account for the effect of the presence of two phases, a two-phase multiplier is introduced in the model and expressed in known parameters such as mass quality, densities, and viscosities of gas and liquid. Validation of the theoretically predicted two-phase multipliers is presented with the experimental results. This present module covers all these aspects in a lucid form so that learners can appreciate the two-phase phenomena and deal with the two-phase problems with confidence.
What's included
16 videos1 assignment
The prediction of the two-phase frictional pressure drop and design of the piping system can also be performed by assuming gas and liquid move separately and simultaneously in the pipe. Certain area of the pipe is occupied by the gas and the remaining area of the pipe is occupied by the liquid. The areas occupied by gas and liquid depend on the flow rates of gas and liquid. There is an existence of an interfacial surface between gas and liquid. The single-phase momentum equation is applied to both gas and liquid separately including the interfacial interactions, and added together to obtain the mathematical expression to predict the frictional pressure drop. The developed model through this idealization is known as the “Separated Flow Model”, SFM. In SFM, the gas and liquid velocities are different, i,e., SFM addresses the relative velocity between gas and liquid. To predict the two-phase frictional pressure drop, the derived mathematical expression is manipulated as the product of a single-phase frictional pressure drop term and a two-phase multiplier to take advantage of single-phase friction factor correlations. The challenge is with the two-phase multiplier. Several investigators suggested the graphical and numerical correlations for two-phase multipliers obtained from experiments. These correlations starting from Lockhart-Martinelli to Friedel are provided in this module. Prediction of two-phase frictional pressure drop using SFM is relatively complex when compared with the HEM. Handling of HEM is easier. Further, HEM closely predicts the frictional pressure drops for all two-phase flow regimes. The deviation from the actual pressure drops is mainly due to the no-slip assumption between gas and liquid phases. The inclusion of slip between gas and liquid in the mathematical expression obtained from HEM; further can predict the pressure drops more closely and the prediction can be within the accepted percentage of error. This is what exactly is done in the “Drift Flux Model, DFM”. The void fraction in DFM is expressed in terms of the phase distribution parameter and superficial velocities of gas and two-phase mixture. Several correlations are suggested by the investigators to determine the void fraction as a function of the phase distribution parameter along with other known parameters are provided in this module. Therefore, this module demonstrates SFM, DFM, and all correlations to predict the total static pressure drop of a given two-phase flow, flowing through an inclined pipe and enables the learners to grasp easily the techniques involved in SFM and DFM and brings confidence in them to deal with the two-phase piping design.
What's included
20 videos1 assignment
This module exclusively covers the two-phase total static pressure drop predictions through individual pipe fittings, piping systems alone, and finally piping networks. Applied the Homogeneous Equilibrium Model and Separated Flow Model together with the Energy Equation to develop the mathematical expressions to determine the total static pressure drop across a sudden enlargement and sudden contraction. This is a good demonstration of applying all the “two-phase models” such as HEM, and SFM to determine the total static pressure drop. While developing the mathematical expression for the total static pressure drop across an orifice, only the Homogeneous Equilibrium Model is used. The methodology is explained for “how to obtain the mathematical expression for total static pressure drop using the Separated Flow Model”. HEM overpredicts the pressure drop across the orifice and hence, suggested corrections in the parameters and methods are included in this module to predict the pressure drop across the orifice more accurately. An orifice is a common device used in the piping systems for both metering and meeting the required pressure drop and hence, accurate prediction is highly expected. Demonstration of pressure drop predictions using all techniques and suggested correlations and methods through solving practical problems is included in this module. Pressure drop predictions across nozzle, venturi, bends with different radius of curvature to diameter ratios, and valves are covered. Two-phase pressure drop in piping networks is complicated and the involvement of pipe fittings further complicate the determination of the two-phase pressure drops in piping networks. A good number of practical problems involving most of the pipe fittings are solved to demonstrate how to predict the two-phase pressure drops. This module is intended to mostly apply all two-phase models, techniques, methods, and suggested correlations to make the learners more conversant with the two-phase phenomena and uplift their confidence levels.
What's included
18 videos1 assignment
Earn a career certificate
Add this credential to your LinkedIn profile, resume, or CV. Share it on social media and in your performance review.
Instructor

Offered by
Explore more from Mechanical Engineering
- Status: Free Trial
L&T EduTech
- Status: Free Trial
L&T EduTech
- Status: Free Trial
L&T EduTech
- Status: Free Trial
L&T EduTech
Why people choose Coursera for their career





Open new doors with Coursera Plus
Unlimited access to 10,000+ world-class courses, hands-on projects, and job-ready certificate programs - all included in your subscription
Advance your career with an online degree
Earn a degree from world-class universities - 100% online
Join over 3,400 global companies that choose Coursera for Business
Upskill your employees to excel in the digital economy
Frequently asked questions
To access the course materials, assignments and to earn a Certificate, you will need to purchase the Certificate experience when you enroll in a course. You can try a Free Trial instead, or apply for Financial Aid. The course may offer 'Full Course, No Certificate' instead. This option lets you see all course materials, submit required assessments, and get a final grade. This also means that you will not be able to purchase a Certificate experience.
When you enroll in the course, you get access to all of the courses in the Specialization, and you earn a certificate when you complete the work. Your electronic Certificate will be added to your Accomplishments page - from there, you can print your Certificate or add it to your LinkedIn profile.
If you subscribed, you get a 7-day free trial during which you can cancel at no penalty. After that, we don’t give refunds, but you can cancel your subscription at any time. See our full refund policy.
More questions
Financial aid available,